Toyota's JIT Revolution
|
|
ICMR HOME | Case Studies Collection
Case Details:
Case Code : OPER006
Case Length : 12 Pages
Period : 1990 - 2002
Organization : Toyota
Pub Date : 2003
Teaching Note : Available
Countries : Japan
Industry : Automobiles
To download Toyota's JIT Revolution case study (Case Code: OPER006)
click on the button below, and select the case from the list of available cases:
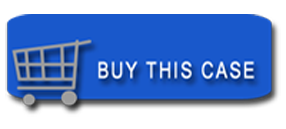
Price:
For delivery in electronic format: Rs. 300;
For delivery through courier (within India): Rs. 300 +Shipping & Handling Charges extra
» Operations Case Studies
» Case Studies Collection
» ICMR HOME
» View Detailed Pricing Info
» How To Order This Case » Business Case Studies » Case Studies by Area
» Case Studies by Industry
» Case Studies by Company
Please note:
This case study was compiled from published sources, and is intended to be used as a basis for class discussion. It is not intended to illustrate either effective or ineffective handling of a management situation. Nor is it a primary information source.
Chat with us

Please leave your feedback
|

<< Previous
Excepts
Just-In-Time Production System
Developed by the Japanese, the JIT production system was one of the most
significant production management approaches of the post World War II era. The
system comprised a set of activities aimed at increasing production volume
through the optimum use of inventories of raw materials, work-in-process, and
finished goods. In a JIT production system, a workstation gets a part just in
time, completes its work and the part is moved through the system quickly.
JIT was based on the principle of producing only what is needed and nothing more
than needed. The Japanese believed that anything produced over the quantity
required was a waste...
|
|
JIT in Toyota
In the early 1930s, the technology used by American automobile companies was
superior to that used by Japanese companies. Kiichiro therefore decided to
learn new automobile production techniques from American manufacturers. He
soon realized that to catch up with the Americans, he had to master basic
production techniques. He then reorganized the production system in Toyota
in a unique way. This reorganization eventually led to the development of
JIT concept...
|
Future of JIT
Although many automobile companies around the world adopted JIT, the
system was far from perfect and difficult to implement. It was based on
the key assumption that sources and channels of supply were reliable and
dependable at all times. Analysts felt that it did not take into account
the possibility of labor strikes at automotive plants. Moreover, JIT
involved high set up costs and Special training and reorganization of
policies and procedures in the company were necessary to implement JIT.
The supplier relations of the company also needed to be improved to
ensure timely delivery. In the absence of good supplier relations, JIT
increased the risk of inventory shortage... |
Exhibits
Exhibit I: Toyota - Business Results (Consolidated, US GAAP)
Exhibit II: Comparison between JIT and Non-JIT Systems
Exhibit III: Toyota's Kanban Philosophy Vs Western Manufacturing Philosophy
Exhibit IV: Plant Productivity
Exhibit V: Productivity Comparision of Different Auto Manufacturers
|
|